
1. Metal Mold Production
Metal mold, usually aluminum, is designed and produced according to the drawings and requirements of the desired casting. The cavity created in the mold will create the same size and structure as the desired casting piece, and a wax model model will be produced.
|
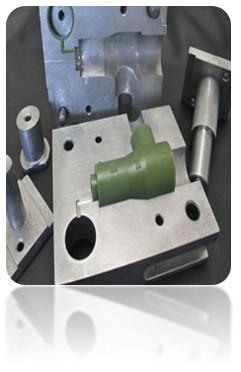
2. Wax Injection
Also known as mold formation, wax casting patterns are created by injecting molten wax into the metal mold above.
|
3. Wax Assambly
The wax patterns are then attached to a gate system, which is usually a series of channels through which molten metal flows into the mold cavity. After that, a tree-like structure suitable for mass production is formed.
|
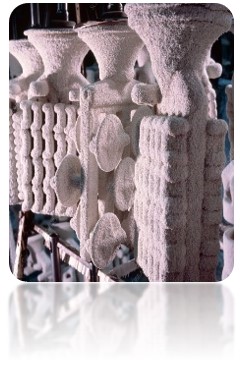
4. Ceramic Mold Production
The investment cast outer shell housing is created by dipping into a ceramic bath and then immediately coated with sand several times.
|
5. Autoclave Oven
(De-Waxing)
To create the inner cavity of the investment casting, waxes are melted in the autoclave furnace and the outer ceramic shell is obtained. The gaps are just the same gap as the castings requested
|
6. Burning and Sintering Furnace
In order to burn the wax residues left in the ceramic waxes that are emptied in the autoclave and in order for the ceramic molds to gain strength, the ceramic molds are kept in high temperature furnaces.
|
7. Casting
Electric furnaces are used to melt steel from scrap, and metal casting is done by adding the necessary alloys or additional components required to achieve the desired final standards and specifications.
|
8. Cutting and Grinding
After the metal cools and solidifies, the castings are individually ground and deburred. Mine entrances are sanded and if necessary straightening is applied to the parts.
|
9. Sandblasting and Finishing
In order to completely remove the sand and oxides, the parts are sandblasted first with drum blasting and then hand sandblasting to obtain a beautiful surface appearance.
|
10. Quality Control and Packaging
Finally, the parts are checked visually and dimensionally, and the faulty parts are sorted out. Checked parts are packed and made ready for shipment.
|